The Truth Behind Why McDonald’s Ice Cream Machines Keep Breaking
Too much mix in the hopper or not enough? Lid off or just maintenance? Everyone knows McDonald's ice cream machines are always broken, but what's the truth?
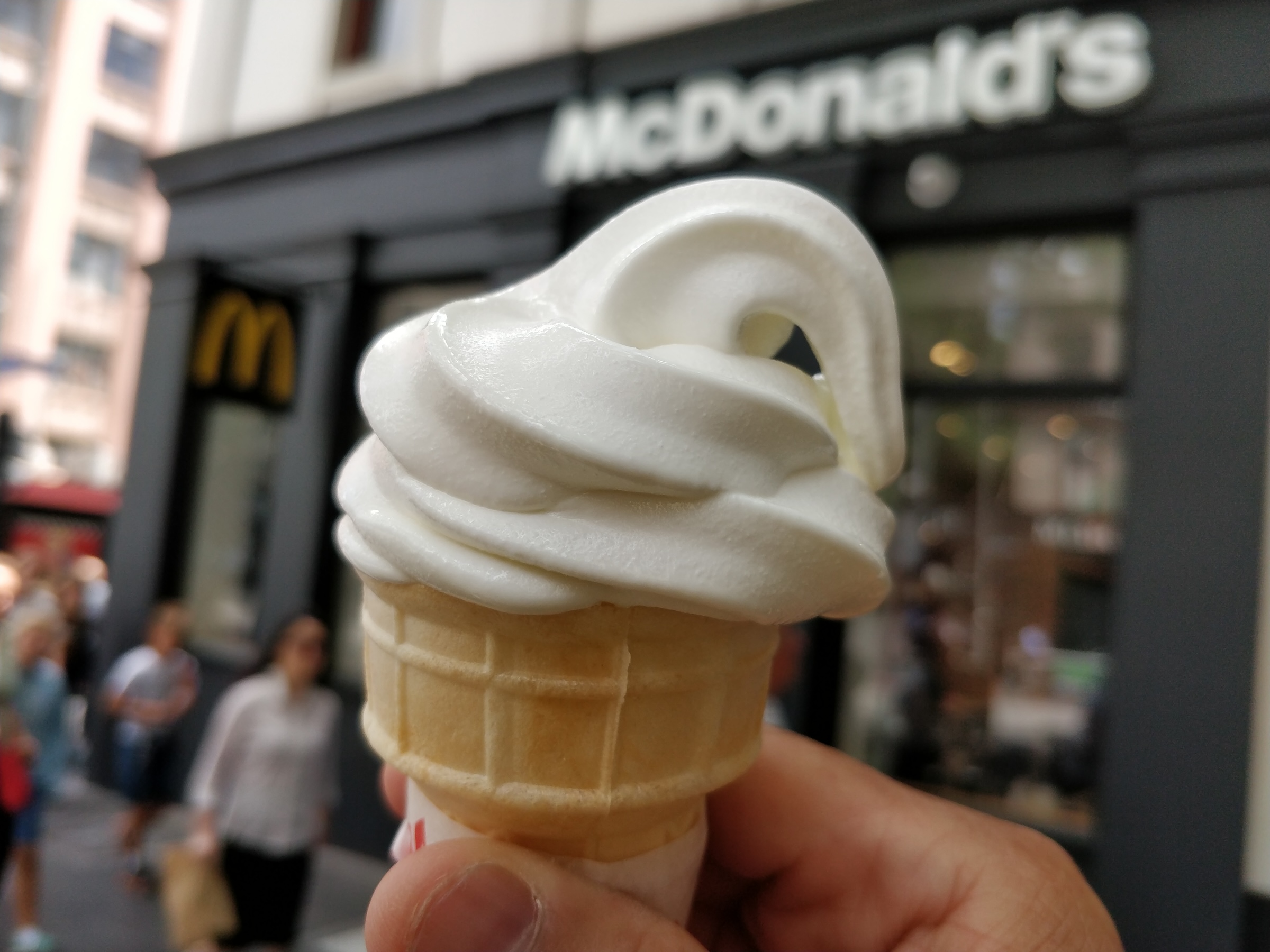
McDonald’s is a household name for many reasons. With 36,000 restaurants in over 100 countries around the world, McDonald’s is known for their iconic clown mascot (Ronald McDonald) as well as a host of other characters, McDonald’s is an American cultural symbol.
McDonald’s has a global brand reputation for consistency and reliability — which makes the questionable availability of McDonald’s soft serve ice cream baffling.
Much has been written about the availability of soft serve at McD's, but what's the truth? Let's take a closer look, including a new perspective from a McDonald's franchise operator.
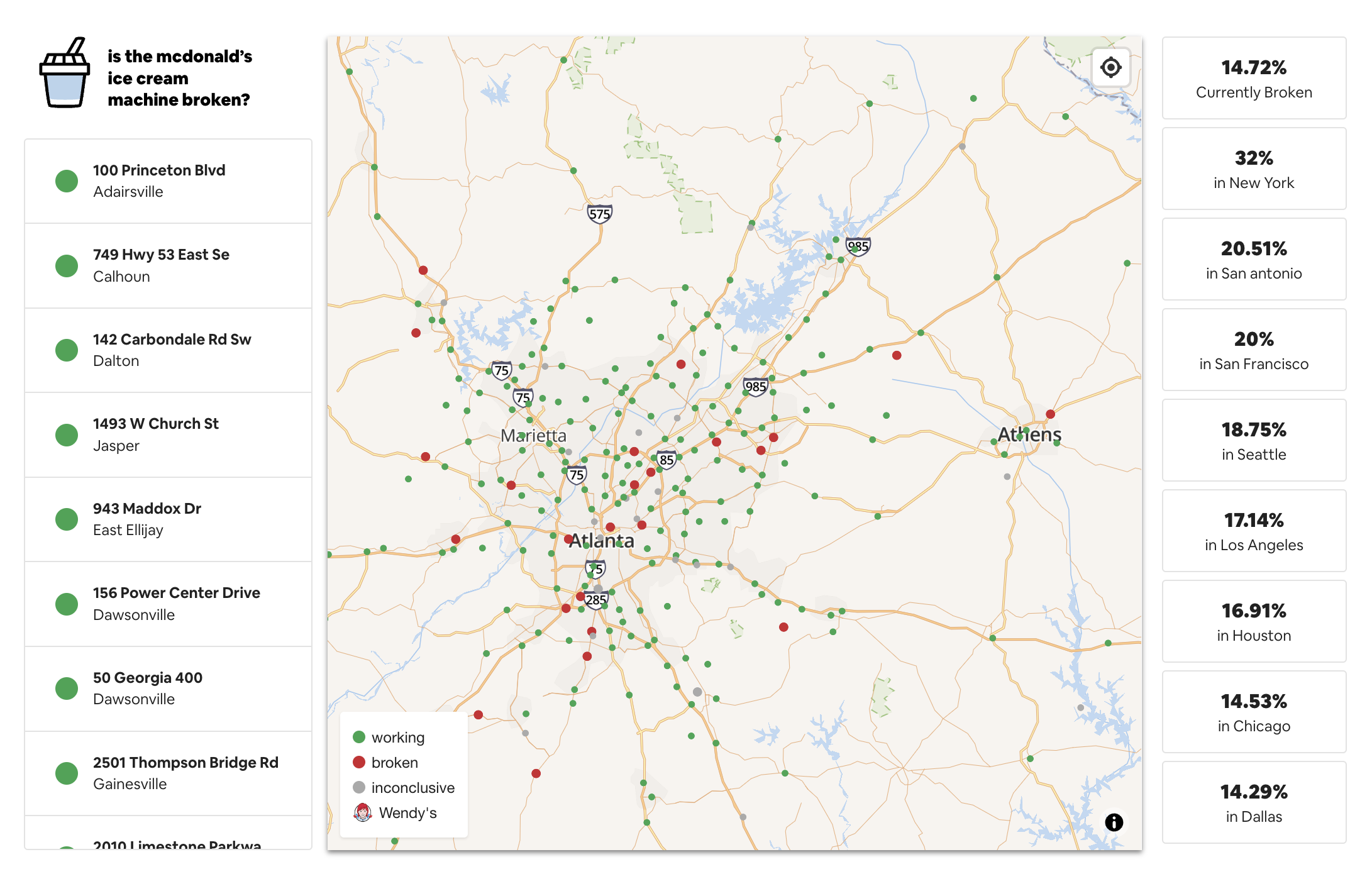
McDonald's (In)famous Ice Cream
Sixty percent of McDonald’s desserts rely on its ice cream machine. Over half of its dessert menu is off the table when the machine is broken. McDonald’s ice cream machines are broken so often that fans of the soft serve have created tools like McBroken to track ice cream availability — and avoid drive-thru disappointment.
Yes, McBroken.
McBroken tracks the status of McDonald’s ice cream machines by placing online orders for sundaes. If the online order is accepted, the restaurant location is assigned a green “working” status. If not, the tool assigns a red “broken” status, warning ice cream customers to try another location to fulfill their sweet tooth craving.
McBroken was created by @rashiq in 2020.
At time of writing, 14.72% — that’s about 1 in 7 — McDonald’s ice cream machines were broken according to the site. Many articles have been written (even YouTube videos published) that detail why broken soft serve machines at McDonald’s are such a common occurrence. Churns out, the truth is complicated. But in order to unswirl this mystery, we must start with detailing how the story commonly goes.
It begins with an exclusive supplier relationship between McDonald’s and Taylor Company, a soft serve ice cream machine manufacturer.
How Device Maintenance and Repair Service Exclusivity Causes Problems
McDonald’s first partnered with Taylor Company in 1956 to provide soft serve ice cream machines for every McDonald’s restaurant. The exclusive relationship continued for over 60 years until it was terminated in 2017. The Taylor Company even developed a machine specifically for McDonald’s — the C602 model.
How does an exclusive supplier relationship lead to an influx of broken ice cream machines?
Word is that, up until recently, only Taylor Company technicians were authorized to repair Taylor Company machines. Taylor Company technicians were the only technicians that could interpret error codes and get past software locks put in place to prevent outside contractors or machine owners from doing their own maintenance. McDonald’s franchise owners needed Taylor Company technicians to diagnose every problem with the soft serve machine and make the appropriate repairs. Even instruction manuals did not include information that would allow McDonald’s employees to attempt fixes.
In the event a tech is needed from the Taylor Company, one may or may not be available to repair a machine in a timely manner. A broken machine would keep ice cream off the menu until authorized maintenance could be performed.
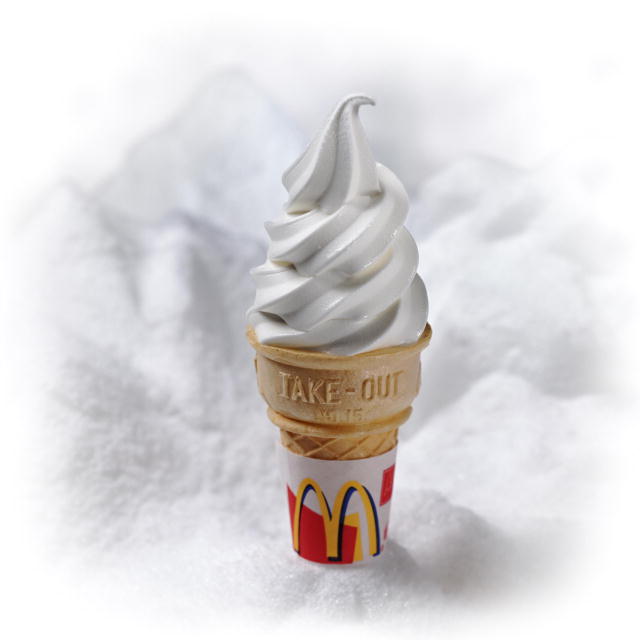
A Legal Fight to Save Soft Serve
McDonald’s and Taylor Company ended their exclusive agreement in 2017. Still, many franchise owners continue to use the exclusive-to-McDonald’s machines. So in 2019, a third-party startup, Kytch, released a device to help franchise owners determine if the machine needed maintenance — or if there was a simpler solution. For example, stop accidentally leaving the lid off the hopper, or you need to add more ice cream mix into the hopper. Or you’re adding too much ice cream mix to the hopper!
(The hopper is where the ice cream mix is stored cold in a liquid state.)
What the Kytch device did was decode error messages on Taylor Company machines and send diagnostic data to owners to improve monitoring. It was in high demand by McDonald’s franchisees too — that is, until they received an email from McDonald’s calling the device a cybersecurity risk and strongly recommending it be removed. (We'll share the "why" from one operator below.)
Later, Taylor Company would release its own similar device.
McDonald's shutdown of the Kytch device removed the startup’s customer base overnight. Kytch filed a lawsuit against Taylor Company. Though Kytch would lose the lawsuit in the end, the high-profile case brought the matter to the attention of the Federal Trade Commission (FTC) and the Department of Justice (DOJ) Antitrust Division.
Extending Right to Repair
In 2021, the FTC began to investigate McDonald’s and Taylor Company for recurring issues with ice cream machines. Three years later in March 2024, the FTC and DOJ filed a comment with the U.S. Copyright Office recommending an extension of existing right to repair laws that would apply to commercial and industrial equipment.
Their reasoning? The inability to hire third parties to perform repairs limits competition, making maintenance more costly and leading to lost revenue.
Right to repair laws prevent manufacturers from restricting customers’ ability to repair or maintain owned products. In the case of McDonald’s ice cream machines, right to repair laws prevent Taylor Company from setting its authorized technicians up as the only resource to fix a broken machine.
Extending the right to repair to commercial equipment gives McDonald’s ice cream machine owners the option to call on cheaper third-party technicians for repairs, giving them more control over when and how long a machine stays broken.
A Win for Third Party Technicians and Devices
In October 2024, the U.S. Copyright Office granted an exemption allowing third parties to bypass manufacturer-implemented software locks to diagnose problems, perform maintenance, and repair broken commercial equipment — including McDonald’s ice cream machines. The exemption went into effect on October 28, giving McDonald’s franchisees more freedom in managing, monitoring, and repairing their machines.
The exemption creates an opportunity for third-party repair technicians as well as for companies following in Kytch’s footsteps to create complimentary devices for machine management. McDonald’s franchises are now empowered to implement remote monitoring and management ([[RMM]]) solutions to track machine performance and proactively identify issues. New connected product innovation will likely follow.
Going forward, ice cream lovers should be dealing with less frustration in the drive-thru as diagnostic tools, [[connected products]], and other RMM solutions give McDonald’s ice cream machine owners and operators faster insight into issues. And third-party repair technicians can be relied upon to keep the soft serve flowing.

Insights from a McDonald's Insider: The Cold, Soft Truth?
Turns out there's more to the story.
Recently, a franchise operator known on X as @McFranchisee shared their insider perspective on the ice cream machine saga. McFranchisee explains that franchisees are, in fact, trained to fix the ice cream machines themselves, "YES, we can fix the machines ourselves." (Here's a link to training courses, in fact.)
Regarding downtime, this operator points out that the machines require nightly pasteurization for safety. Additionally, every 14 days the ice cream machines receive a thorough cleaning. "Every night, our machines go through a pasteurization mode ...This ensures food safety." When machines go down intentionally, this necessarily takes them "offline" for customers.
Meanwhile, when real breakdowns occur, repairs can be delayed whether for receiving parts and or technician scheduling.
Most importantly, @McFranchisee points out that downtime is most noticeable at McDonald's because any given franchise only has one ice cream machine — there is no backup.
Meanwhile, the machines aren't cheap. According to @McFranchisee, a new Taylor Company machine (the FDM) costs about $30,000 new and an ongoing maintenance fee of $700 quarterly, promising 99% uptime.
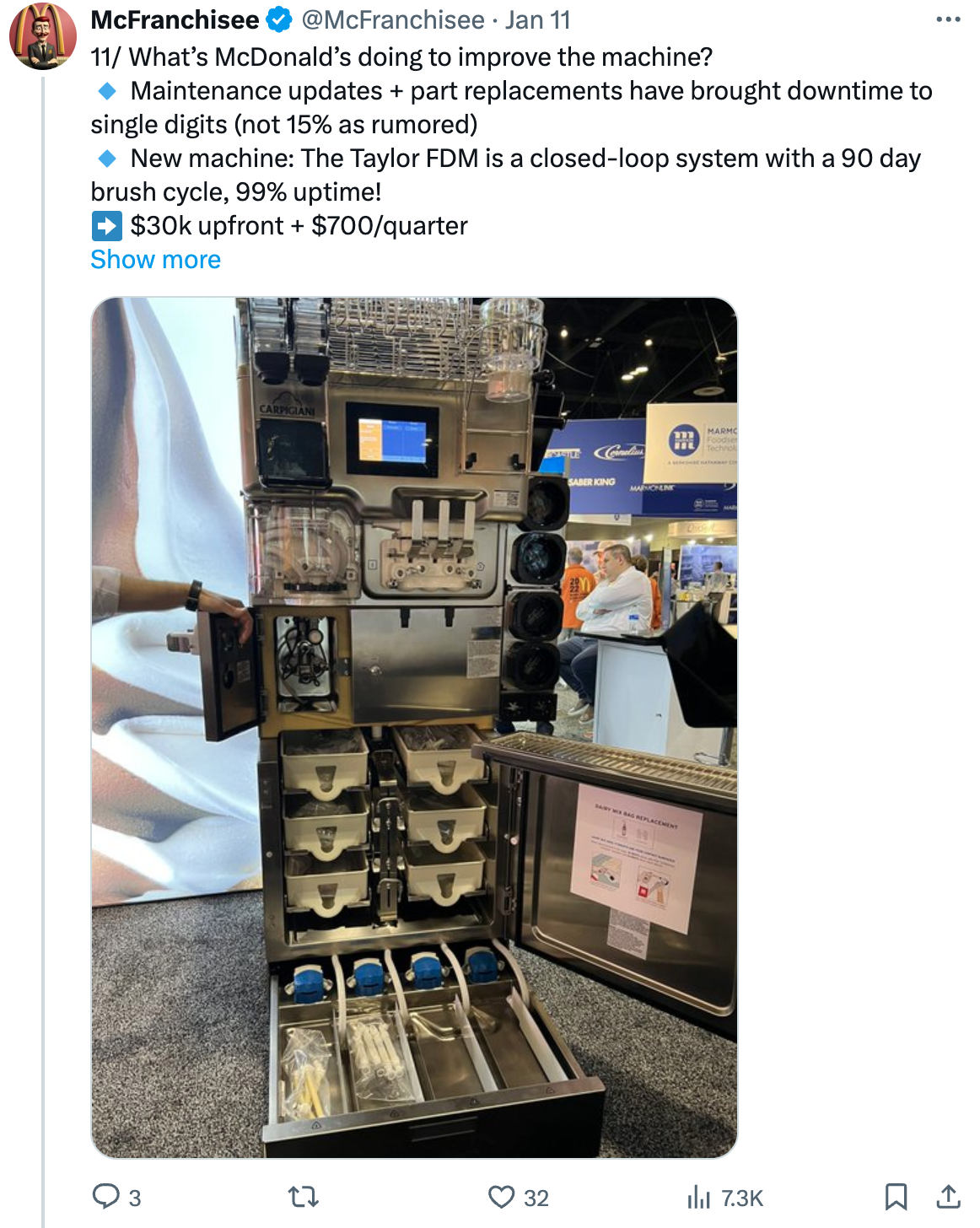
Now, contrary to popular narratives, the Taylor Company machines aren't the only machines available, "It’s FALSE that Taylor is the only machine we can use." Italian company Carpigiani has offered machines to franchises for more than twenty years. McFranchisee goes on to note, "Why not switch to Carpigiani? It’s a better machine, but its service network is not good."
As for Kytch, the diagnostic device mentioned earlier, the product was initially priced at $120/year per store, but over time the price tripled, impacting its use.
All told, this franchise operator believes the ice cream drama is overstated. As they put it, "IMO, the ice cream machine drama is overplayed."
Regular cleaning and the ability to self-repair mean issues are less frequent than perceived, and the costs reflect the investment in quality service for customers.
Do you live on the edge of endpoint management?
Discover how global brands and businesses manage their connected product ecosystems. Get the inside-scoop from the hidden architects and teams who ensure their remote devices never go down.
Subscribe to the Canopy Insights newsletter.
Do you live on the edge of endpoint management?
Discover how global brands and businesses manage their connected product ecosystems. Get the inside-scoop from the hidden architects and teams who ensure their remote devices never go down.
Subscribe to the Canopy Insights newsletter.
What McDonald’s Ice Cream Machine Saga Teaches Us About QSR Technology
The McDonald's ice cream machine saga is more than just a quirky story about a broken dessert machine — it’s a case study in how a seemingly minor component in a Quick Service Restaurant (QSR) operation can turn into a huge, newsworthy story.
It's a study in how downtime can hurt revenue and customer satisfaction too.
Tools like McBroken poke fun while offering a service to customers — even if that service is to tell would-be McDonald's customers about Wendy's. (The McBroken map lists Wendy’s locations alongside McDonald's).
Most surprisingly, McBroken didn’t just provide transparency to consumers. The website made the ice cream machine issue impossible to ignore for McDonald’s. It even gave the company a strange form of remote monitoring. If you're not familiar, remote device monitoring makes it easy to observe the status of connected products — everything from self-service kiosks to point-of-sale (POS) systems to cameras to every kind of restaurant technology. Using remote device management software (like Canopy), technical support teams can manage those products and devices, troubleshooting remotely and avoiding costly on-site repairs. It can even help with [[device lifecycle management]].
Now that the U.S. Copyright Office’s right to repair exemption has gone into effect (as of October 2024), McDonald’s franchisees have more tools at their disposal to prevent machine breakdowns. The ability to monitor, diagnose, and repair machines through third-party technicians should lead to less downtime, more ice cream sales, and happier customers.
The stakes are high. Because while a broken ice cream machine may seem a minor issue, failing technology means lost revenue, unhappy customers, and businesses getting their just deserts.
Finally, check out our follow-up article on how McDonald's franchise operators think about QSR technology costs and technical support — and how McDonald's can balance innovation with delivering an experience customers love.
Interested in how other restaurants manage their restaurant technology, check out Chick-fil-A's advanced approach to computing at the edge or learn about how the Domino's Pizza Pulse POS manages ordering for some 20,000 restaurants.